Why It Matters to Us
We recognize that climate change is the preeminent sustainability issue affecting all industries today and in particular, natural gas producers like EQT. Furthermore, the makeup of the future energy mix has significant environmental, social and economic ramifications for the United States and will influence future demand for — and consequently the price of — natural gas. We seek to remain informed on climate science and we are committed to understanding both how climate change affects our business and how EQT impacts climate change.
As the largest natural gas producer in the United States, we are particularly conscious of methane emissions. While natural gas produces significantly less carbon dioxide compared to other fossil fuels, methane emissions are a strong concern for our stakeholders. We maintain strong management systems to effectively drive down our emissions and lessen our impact, and we maintain and monitor best management practices to minimize greenhouse gas (GHG) emissions while making improvements to reduce our climate impact. As a result, our operations have one of the lowest GHG emissions intensities in the country, and our methane emissions intensity is significantly below the 2025 Production segment target set by the ONE Future Coalition, a group of 38 natural gas companies working together to voluntarily reduce the methane emissions intensity across the natural gas value chain to 1% (or less) by 2025.
In conjunction with publishing this report, we announced our establishment of the following aggressive emissions targets for our Production segment operations:
Achieve net zero Scope 1 and Scope 2 GHG emissions by 2025
Reduce our Scope 1 GHG emissions intensity to below 160 MtCO2e/Bcfe (representing an approximately 70% reduction compared to 2018 levels) by 2025
Reduce our Scope 1 methane emissions intensity to below 0.02% (representing an approximately 65% reduction compared to 2018 levels) by 2025
For more information on our emissions targets, see GHG Emissions and Targets.
Strategy
In recent years, the effects of climate change on the planet and economy have become more apparent, and increased stakeholder scrutiny of climate change management, in combination with rapidly changing regulations, have brought this topic to the forefront of the business environment.
As the nation’s largest producer of natural gas, both the effects of climate change as well as the prevailing views on how to optimally curb the impact thereof have the potential to meaningfully impact EQT. Increased adverse weather events could affect our ability to operate on schedule, impact service providers and increase the difficulty of complying with regulations directed at mitigating weather events, such as run-off restrictions and operations in severe heat. In addition, the impacts of climate change also have the potential to affect EQT financially. As investors continue to focus on climate change management and mitigation, demand for natural gas could decrease, reducing the price we receive for our product. Furthermore, our access to capital funding could be restricted if we are unable to articulate and execute our sustainable development strategy.
Given the dynamism in the debate about the optimal manner to accelerate a sustainable path to a low carbon future, our vision for how we can best contribute to countering the effects of climate change first centers on positioning our company to be able to react nimbly and effectively as data continues to emerge and technologies continue to develop. To that end, we have spent considerable time and resources building a technological and cultural foundation within our company to allow us to adjust our corporate strategy as the balance of risks and opportunities fluctuate. We have begun to better integrate climate change into our business strategy, incorporating emissions footprint considerations into the foundation of our business. At the corporate level, we built a proprietary emissions model that will be integrated with our financial model, allowing us to layer-in different cost-of-carbon scenarios in making capital allocation decisions. Additionally, at the asset level, we are currently layering into our digital work environment the functionality to attribute emissions down to the well level, allowing us to optimize our capital expenditures by investing in the parts of our business that present the best return on investment for reducing greenhouse gas (GHG) emissions.
Second, while we are positioning our company to evolve, our strategy is built on two key beliefs:
- Natural gas is critical to accelerating a sustainable pathway to a low carbon future
- Natural gas, and in particular Appalachian natural gas, will differentiate itself from oil
As such, two of the three prongs in our long-term strategy focus on maintaining a long-term interest in natural gas assets, continuing to improve on our track record for strong financial performance concurrent with significant emissions reduction (Evolve) and expanding the reach of those benefits over a broader base of assets (Consolidate).
As a part of the energy mix, natural gas consumption will be directly impacted not only by the rate at which climate change effects are seen, but also by prevailing views on the best methods to mitigate future impacts of climate change. The consumption of, and demand for, natural gas can be both negatively and positively affected by either of these, in particular as it pertains to the relative market share of energy supply for power, and thus risks and opportunities exist in what we believe will be an increasingly dynamic environment.
And third, while we anticipate maintaining a long-term interest in natural gas assets, we see the potential to meaningfully participate in energy transition opportunities. To this end, in 2021 our Board of Directors authorized the creation of an innovation fund, establishing a $75 million pool of capital that we can use to develop, invest in, partner with and acquire new ventures or otherwise pursue initiatives aligned with our environmental, social and governance (ESG) strategy through 2025. Our guiding principles on allocating capital to new ventures generally center on (i) promoting natural gas demand and participating in the low carbon transition, (ii) leveraging our assets, skillsets and relationships to capture opportunities, (iii) targeting opportunities for meaningful scale and growth, (iv) deploying proven technology and (v) improving our ESG reputation. For more information on our corporate strategy, please see Sustainable Value Creation.
While we have not yet conducted a formal scenario analysis to determine potential impacts of climate-related risks and opportunities, we plan to layer our bottoms-up analysis of natural gas supply over different demand forecasts and pricing scenarios to better understand our climate-related risks and opportunities.
For more information about climate-related risks, see pages 17-19 of our 2020 Form 10-K.
Reducing Methane and Other Emissions
Our emissions depend greatly on the type and amount of field activity conducted at any given time and vary on an annual basis. We review our Scope 1 emissions inventory on a source-by-source basis to determine areas of opportunity and to monitor our overall impact.
Our Scope 1 emissions primarily originate from our operations and fleet transportation. Fuel combustion and natural gas-driven pneumatic equipment are currently the largest contributors to our Scope 1 emissions, and we therefore dedicate resources to improving these processes and equipment. We outline our environmental guidelines and data tracking expectations in our Environmental, Health and Safety (EHS) Management System.
We outline our approach for each source below. Our primary emissions reduction activities include:
- Strategic site design
- Leak Detection and Repair Program
- Preventing venting and flaring
- Preventing releases during well unloading
- Using glycol pumps on dehydration units
Our focus on implementing innovative technologies, best management practices and aligned policies over the past several years has directly resulted in decreasing our methane emissions intensity. We regularly review technologies to see if they can cost-effectively reduce our emissions in the short term (read more about this process in Technological Evolution). For example, pursuant to our pilot project with Project Canary to certify a portion of our natural gas under the IES TrustWell Certification, we have installed Project Canary’s “Canary X” emissions monitoring devices on two of our well pads to measure methane concentrations at the site level every second and communicate the results to a cloud database every minute. The data collected from the emissions monitoring devices is assessed on over 300 metrics related to production practices, including air, land, water and waste management, as well as drilling and completion processes, and ultimately used to assign a TrustWell Certification rating to the participating well pads.
We also actively participate with ONE Future and The Environmental Partnership, both of which seek to improve the industry’s environmental performance. Using a science-based approach, ONE Future, a collaborative group of natural gas companies, has set a 2025 target for methane emissions intensity for the industry at or below 1%, and a target of 0.28% for the Production segment and 0.08% for the Gathering and Boosting segment. We outperform the ONE Future methane intensity targets for the industry and our applicable operating segments, as shown below.
Methane Intensity
EQT Methane Intensity — Production Segment Emissions[1] | ONE Future Production | EQT Methane Intensity — Gathering and Boosting Segment Emissions[2] | ONE Future Gathering and Boosting Segment Methane Intensity Target | |
2018 | 0.06% | 0.28% | N/A | 0.08% |
2019 | 0.06% | N/A | ||
2020[3] | 0.054% | 0.076% |
Through The Environmental Partnership, we collaborate with other upstream companies to evaluate best management practices for reducing emissions. Resources provided by The Environmental Partnership include programs designed to reduce methane emissions and volatile organic compounds using proven cost-effective technologies.
EQT’s 2020 methane intensity for its Scope 1 Production segment emissions is approximately 81% lower than the 2025 target set by ONE Future for the Production segment.
Site Design
We currently use pneumatic level switches and liquid level controllers to set thresholds and control motor valves for managing fluid in vessels such as separators, scrubbers and contact towers. For example, we operate thousands of pneumatic controllers and level switches that regulate gas/liquid separation volumes or activate shutdowns when high or low liquid levels occur.
Air, natural gas, electricity or other supply media can power pneumatic controllers and level switches, with natural gas being the most common power source for pneumatic devices. The U.S. Environmental Protection Agency (EPA) classifies natural gas pneumatic controllers and level switches into three categories: continuous high-bleed, continuous low-bleed and intermittent-bleed. High-bleed pneumatic controllers are significant sources of methane emissions when compared to low- or intermittent-bleed controllers.[4]
Replacement of a high-bleed controller with a low-bleed or intermittent-bleed controller results in a reduction of GHG emissions by approximately 96% and 64%, respectively.[5] We do not currently operate any high-bleed pneumatic controllers; we currently use only low-bleed and intermittent-bleed pneumatic controllers in our production facilities.
In 2020, we conducted an inventory of our Scope 1 emissions to determine which of our activities are the primary drivers of our GHG emissions. Based on our analysis, we determined that a substantial portion of our Scope 1 emissions are generated from natural-gas-powered pneumatic devices.
Although the vast majority of pneumatic devices used in the oil and gas industry are powered by natural gas, alternative available options are powered by nitrogen, compressed air, or other non-GHG emitting sources — each of which eliminates emissions from the pneumatic device with, in certain instances, de minimis increases in emissions attributable to power generation.
Beginning in 2020, we began an initiative to replace all natural-gas-powered pneumatic equipment in our operations by 2025. We believe this can be accomplished with only a limited capital outlay, which we believe is unique in the industry and is driven by the high productivity-to-well (and site) ratio of our asset base.
Leak Detection and Repair Program
One of the most significant investments we have made to reduce emissions releases has been our investment in leak detection and repair (LDAR) surveys. Going beyond compliance with robust state and federal requirements on air emissions, our LDAR program involves:
- Utilization of optical gas imaging (OGI) technology at all compressor stations, dehydration facilities and unconventional sites for conducting LDAR surveys ranging from monthly to annually, depending on the facility
- A team of EQT employees who have completed a three-day training consisting of classroom and onsite experience with OGI experts, certified to operate gas detection cameras
- Use of three types of OGI cameras, all verified by the manufacturer to meet the EPA’s LDAR requirements under the EPA’s New Source Performance Standards for the Oil and Natural Gas Industry
- Annual auditory, visual and olfactory inspections for each of our conventional wells
- Quarterly mechanical integrity inspections for our conventional wells in Pennsylvania and quarterly visits to conventional wells with storage vessels in West Virginia to perform inspections for gas leaks
- Remote gas detection monitors inside the gas processing units of our unconventional wells that monitor for leaks in real time and that automatically alert EQT’s gas control center to assign a specialist to conduct an inspection
- Leak repairs conducted as soon as reasonably possible
- Resurveying all leak repairs with an OGI camera to confirm the repair was successful
Our standard practice exceeds state and federal requirements related to leak repair procedures, and we are upgrading our management system to track leak repairs at our sites. In 2020, no repairs were delayed beyond the applicable regulatory limits, and more than 92%[6] of all leaks detected in our production operations were repaired immediately.
In January 2021, we entered into a pilot project with Project Canary/IES TrustWell to demonstrate that our natural gas is produced with high environmental and social standards, and that global energy market demand exists and is growing for differentiated energy products. Under the terms of the pilot, Project Canary’s “Canary X” emissions monitoring devices have been installed on two of our well pads to measure methane concentrations at the site level every second and communicate the results to a cloud database every minute. The data collected from the emissions monitoring devices are independently verified and used to issue a TrustWell Certification certifying that gas produced from our participating well pads is “responsibly sourced natural gas.”
We are actively developing plans to increase our usage of next-generation monitoring technologies — such as those employed in our pilot project with Project Canary — across a broader portion of our asset base. While we already employ leading practices in detection, we are driven to constantly improve our ability to identify and quickly address potential emissions incidents.
Leak Detection and Repair Metrics[7]
| 2019 | 2020 EQT | 2020 Chevron Assets |
Total optical gas imagaging surveys | 977 | 675 | 134 |
Total leaking components | 1,058 | 371 | 97 |
Components repaired immediately | 911 | 342 | 80 |
Components repaired within 2 to 15 days | 146 | 29 | 17 |
Components repaired within 15 days | 1 | 0 | 0 |
Venting/Flaring Practices
We use a green completions program to reduce our volume of vented and flared gas during our operations. Green completions technology transfers the natural gas at the wellhead to a separator immediately after well completion as opposed to flaring or venting the gas. Through use of green completions technology, we did not vent or flare any gas during our completions operations in 2020.
During the production phase of a well, our flaring and venting practices differ based on the amount of condensate and oil produced from the well. Generally, the industry considers a “dry gas” well as a well that produces water, methane and ethane but not significant natural gas liquids (NGLs), condensate or oil. A well that consistently produces natural gas in addition to condensate and/or oil is considered a “wet gas” well. Dry gas wells generally have significantly lower emissions when compared to wet gas wells and require less emissions controls. The significant majority of the wells we operate are dry gas wells and no gas is flared in connection with producing from our dry gas wells. To minimize flaring at our wet gas wells, we use various methods of emissions minimization options including the design of closed-vent systems with low-pressure separators, vapor recovery systems and vapor destruction systems.
We leverage best management practices for the installation of pilot-operated valves and latch-down hatches on closed-vent systems, necessitating the installation of low-pressure separators with vapor recovery systems during periods of high production. The valves, hatches and additional separators have significantly improved sealing, reduced leaks and led us to standardize the installation of latch-down hatches on all new installations. We conduct monthly LDAR inspections on these closed-vent systems and condensate sites.
Well Unloading
As a natural gas well ages, “liquid loading” occurs as liquids — primarily water — accumulate in the wellbore. These liquids create backpressure that restricts or stops the gas flow. To restore productivity, multiple approaches can be used to unload the fluid from the wellbore; the simplest is to flow the well to a lower pressure environment, such as an atmospheric tank. As part of our ongoing efforts to minimize emissions, we follow guidance from The Environmental Partnership to reduce methane emissions from well unloading.
If a well only produces through production casing, we install tubing to reduce flow area, allowing the produced gas from the well to efficiently unload the fluid. We install well tubing on an accelerated schedule to limit the amount of venting that occurs from well unloading activities, reducing the amount of methane emissions. We are able to further minimize tank venting by using automated plunger lift equipment in wells with tubing. Where this is not possible, it may be necessary to use a swab rig to mechanically remove fluids from a well to restore flow. For unconventional wells, we have personnel on site while unloading wells. Additionally, we follow the industry best practice of installing plunger lifts one to three years into a well’s life. Each of these methods achieves liquid removal without releasing emissions directly into the atmosphere.[8]
Dehydration Units
To reduce methane emissions during production operations, we use glycol pumps rather than natural gas pneumatic pumps on existing dehydration systems to transfer bulk glycol. These pumps only emit gas embedded within the glycol and do not need to be powered by natural gas pressure, resulting in lower methane emissions. Additionally, to further minimize emissions, our standard protocol is to install condensers on new dehydration regenerator still columns. These units condense volatile liquid organics out of the gas and vapor streams collecting marketable NGLs and minimizing odors and emissions. The resulting emissions are sent to a vapor destruction unit.
Electrifying Our Frac Fleet
As described in Air Quality, we continued to electrify our hydraulic fracturing (frac) fleet in 2020, switching from conventional diesel fleets to electric fleets powered by a natural-gas-fired turbine using EQT-produced natural gas. We project that the implementation of these next-generation electric frac fleets has eliminated over 23 million gallons of diesel fuel from our operations annually. The electrification of our frac fleet also decreases our emissions due to the corresponding reduction in vehicle use that would otherwise be needed to deliver diesel fuel to our well pads.
Transportation
We have operations in multiple states, requiring us to rely on trucks and other fleet vehicles for the transportation of workers and materials to job sites. EQT vehicles drive millions of miles annually, and we actively pursue efficient, cleaner-burning alternatives, such as compressed natural gas (CNG), for our vehicles. In 2020, our focus on centralized development in the core of our operational footprint led to a fleet reduction of approximately 95 trucks, utilizing newer, fuel-efficient, technology-enabled vehicles to further reduce total vehicle miles and associated emissions. Read more about our transportation improvements in Water.
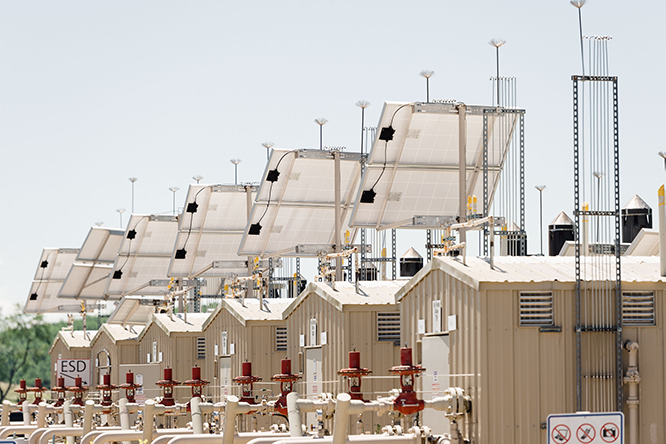
[1] Calculated using ONE Future’s methodology for calculating methane intensity for Production segment emissions. Includes only Scope 1 methane emissions.
[2] Calculated using ONE Future’s methodology for calculating methane intensity for Gathering and Boosting segment emissions. Includes only Scope 1 methane emissions. We did not participate in ONE Future’s calculation of methane intensity for our Gathering and Boosting segment emissions in 2018 and 2019.
[3] 2020 methane intensities are inclusive of emissions from the Chevron Assets. 2020 methane intensities are preliminary — final 2020 calculations are expected to be published by ONE Future in the third quarter of 2021.
[4] Source: 40 CFR 98 Subpart W - Table W-1A
[5] Source: https://www.law.cornell.edu/cfr/text/40/appendix-Table_W-1A_to_subpart_W_of_part_98
[6] Based on EQT historical assets — excluding leaks associated with the Chevron Assets.
[7] Metrics only include optical gas imaging survey data.
[8] https://www.ourenergypolicy.org/wp-content/uploads/2014/04/epa-liquids-unloading.pdf
GHG Emissions and Targets
We monitor and report on operational air emissions as required by state and federal regulations. We gather operational data and calculate emissions annually to comply with emissions inventory requirements in each state where we have operations. For sources subject to the EPA’s Greenhouse Gas Reporting Program, we submit reports to the U.S. Environmental Protection Agency (EPA), where they are validated electronically. We are not subject to any greenhouse gas (GHG) emissions-limiting regulations and seek continuous improvement capabilities in areas that provide the most opportunity for GHG reductions.
Our GHG emissions are broken into three categories or “scopes.” Scope 1 emissions are direct GHG emissions from sources we own or control. Scope 2 emissions are GHG emissions from the generation of purchased electricity consumed in connection with our operations. Scope 3 emissions are all other indirect GHG emissions as a result of our activities, from sources not owned or controlled by us. We explain how we calculate our Scope 1, 2 and 3 emissions in more detail below; however, the Greenhouse Gas Protocol has additional information about how the scopes are defined.
Scope 1 GHG Emissions
We calculate our Scope 1 GHG emissions in accordance with Subpart C (Stationary Fuel Combustion) and Subpart W (Petroleum and Natural Gas Systems) of the EPA Greenhouse Gas Reporting Program. Pursuant to the EPA’s rules and regulations, emissions are reported according to defined “industry segments” as opposed to a single set of emissions at the operator level. There are five industry segments under the EPA’s reporting framework for petroleum and natural gas companies: Production; Gathering and Boosting; Processing; Transmission and Storage; and Distribution. The significant majority of our operations (and consequently our Scope 1 GHG emissions) fall within the Production segment.
In November 2018, we completed the spin-off of Equitrans Midstream Corporation (New York Stock Exchange: ETRN), a separate, publicly traded company formed to hold our former natural gas gathering, transmission, storage and water services businesses (the ETRN Spin-Off). Following the ETRN Spin-Off, we no longer held a material amount of midstream assets, and accordingly, we stopped including our Scope 1 GHG emissions from our remaining limited midstream assets (which fall within the Gathering and Boosting segment) in our ESG Reports following the ETRN Spin-Off.
Although we still only own an insignificant amount of midstream assets, we are disclosing 2018, 2019 and 2020 emissions from these assets as identified below as emissions from the Gathering and Boosting segment. We have no emissions within the Processing, Transmission and Storage or Distribution segments.
Scope 1 GHG Emissions (metric tons CO2e)[1]
PIE CHARTS
Scope 1 Emissions Sources (metric tons CO2e)
Accounting Metric | 2018[2] | 2019 | 2020 (EQT) | 2020 Annualized (Chevron Assets) |
Production Segment Scope 1 GHG Emissions | ||||
Combustion emissions[3] | 466,346 | 202,952 | 215,382 | 50,311 |
Process emissions[4] | 15,615 | 90,591 | 28,507 | 3,333 |
Other vented emissions[5] | 410,122 | 489,983 | 370,090 | 72,831 |
Fugitive emissions[6] | 23,019 | 6,818 | 5,190 | 347 |
Flared hydrocarbons[7] | 0 | 0 | 0 | 0 |
Completions and workover venting emissions | 6,937 | 5,349 | 5,979 | 1,139 |
Total Production Segment Scope 1 GHG Emissions | 922,039 | 795,693 | 625,148 | 127,961 |
Gathering and Boosting Segment Scope 1 GHG Emissions | ||||
Combustion emissions[3] | 48,289 | 58,679 | 38,266 | 3,724 |
Process emissions[4] | 8,625 | 9,569 | 4,914 | 1,867 |
Other vented emissions[5] | 6,028 | 4,716 | 4,468 | 402 |
Fugitive emissions[6] | 10,789 | 10,703 | 1,601 | 0 |
Flared hydrocarbons[7] | 0 | 0 | 0 | 0 |
Total Gathering and Boosting Segment Scope 1 GHG Emissions | 73,731 | 83,667 | 49,249 | 5,993 |
Scope 1 GHG Emissions Intensity[8]
| 2018 | 2019 | 2020 (EQT) | 2020 (Chevron Assets) |
Production Segment GHG Emissions Intensity (Production Segment Scope 1 GHG Emissions (metric tons CO2e) / Gross Production of Hydrocarbons (Bcfe)) | 529 | 440 | 357 | 695 |
Gathering and Boosting Segment GHG Emissions Intensity (Gathering and Boosting Segment Scope 1 GHG Emissions (metric tons CO2e) / Gross Production of Hydrocarbons (Bcfe)) | 42 | 46 | 28 | 33 |
Total Scope 1 GHG Emissions Intensity (Total Scope 1 GHG Emissions (metric tons CO2e) / Gross Production of Hydrocarbons (Bcfe)) | 571 | 487 | 385 | 728 |
Scope 2 GHG Emissions
While we have not historically tracked our Scope 2 GHG emissions (i.e., indirect GHG emissions from purchased electricity to power certain of our operations), we developed a methodology to calculate these emissions in 2020, and are including the data for the first time in this report. A third-party entity, typically a utility, generates these emissions at their facility.
The two prevailing methods for calculating Scope 2 GHG emissions are the market-based approach and the location-based approach. Under the market-based approach, Scope 2 emissions are calculated based on the reporting company’s contracts with electric utilities. Under the location-based approach, Scope 2 emissions are calculated based on the average emissions intensity of the reporting company’s local power grid. We use the location-based approach to calculate our Scope 2 emissions.
Scope 2 GHG Emissions (metric tons CO2e)[9]
| 2020 |
Carbon dioxide (CO2) | 2,796 |
Methane (CH4) | 7 |
Nitrous oxide (N2O) | 11 |
TOTAL | 2,814 |
Scope 3 GHG Emissions
Similar to Scope 2 emissions, we began efforts to track and understand our Scope 3 GHG emissions (i.e., other indirect emissions) in 2020. There are 15 categories of Scope 3 emissions. To fully understand our Scope 3 emissions, for 2020, we calculated our Scope 3 emissions within all 15 categories. We then conducted a materiality assessment to determine which of the 15 categories are material to helping our stakeholders understand our Scope 3 emissions impact.
As is the norm within our industry, the substantial majority of our 2020 Scope 3 emissions were generated from category 11 (use of sold products). As such, we are reporting only Scope 3 emissions from category 11, which is also in line with the industry benchmarking analysis we conducted as a part of our Scope 3 materiality assessment.
Scope 3 GHG Emissions (metric tons CO2e)[10]
| 2020 |
Use of Sold Products (Category 11) | 87,465,365 |
GHG Emissions Targets
As discussed in our Climate Strategy and Sustainable Value Creation, the Evolve aspect of our strategy focuses on realizing the full potential of our current asset base. The purpose of evolution is to distinguish our capabilities from those of our peers, differentiating EQT. In line with that focus, we have set the following short- and medium-term goals for our Production segment operations to keep us on track:
Achieve net zero Scope 1 and Scope 2
GHG emissions by 2025
Reduce our Scope 1 GHG emissions intensity to below 160 MtCO2e/Bcfe (representing an approximately 70% reduction compared to 2018 levels) by 2025
Reduce our Scope 1 methane emissions intensity to
below 0.02% (representing an approximately 65%
reduction compared to 2018 levels) by 2025
To further demonstrate that our impact on climate change is a priority for EQT, we have tied our 2021 incentive compensation program, under which our executives and other employees participate, to a reduction in our Scope 1 GHG intensity.
As is demonstrated by our emissions intensity targets, we are planning to achieve our goal of net zero Production segment Scope 1 and 2 emissions by 2025 primarily through operational improvements. In 2020, we conducted an inventory of our Scope 1 emissions to determine which of our activities are the primary drivers of our GHG emissions. Based on our analysis, we determined that a substantial portion of our Scope 1 emissions are generated from one piece of equipment — pneumatic devices.
Although the vast majority of pneumatic devices used in the oil and gas industry are powered by natural gas, alternative available options are powered by nitrogen, compressed air, or other non-GHG emitting sources — each of which eliminates emissions from the pneumatic device with, in certain instances, de minimis increases in emissions attributable to power generation. We believe that we can replace our natural-gas-powered pneumatic devices across our asset base in their entirety with only a limited capital outlay, which we believe is unique in the industry and is driven by the high productivity-to-well (and site) ratio of our asset base. Doing so will constitute a substantial portion of our emissions reduction goals.
[POTENTIAL PLACEHOLDER FOR IMPACT OF ELIMINATING PNEUMATICS ON GHG AND METHANE EMISSIONS CHARTS - PER EQT]
While we are already operating at an industry-leading emissions intensity level — in part driven by prior adoption of emissions-friendly operational technologies like electric frac crews and hybrid drilling rigs — we fully anticipate additional opportunities for operational improvements above and beyond our pneumatic device replacement initiative, albeit of lesser impact, to contribute to achieving our net zero goal.
As we prioritize emissions reduction opportunities, we place a premium on true emissions reduction. This is not only when making capital allocation decisions for emissions elimination programs versus generating offsets and purchasing credits, but also in how we prioritize projects that will support actual emissions reductions versus emissions reported pursuant to EPA guidance. For example, starting in 2020, we began a process to replace our natural-gas-powered pneumatic devices on newer well sites. Our internal research has shown that actual annual emissions attributable to pneumatic devices during the first two years of the productive life of a well are roughly equal to the actual emissions for the remaining balance of the well’s life. Importantly, while these early life pneumatic device emissions likely exceed the flat annual emissions attributed under EPA guidelines (which apply a single emissions factor regardless of the life of the well), we also found that EPA guidelines result in inflated emissions for the remainder of the life of the well.[11] As such, when we initiated our pneumatic device replacement program in 2020, we began by targeting all new development and all sites that were within their first two years of production. Quite simply, our goal is to reduce actual emissions, not “desktop” emissions. Further to that end, we are actively developing plans to increase our usage of next-generation monitoring technologies — such as those employed in our pilot project with Project Canary/IES TrustWell — across a broader portion of our asset base. While we already employ leading practices in detection, we are driven to constantly improve our ability to identify and quickly address potential emissions incidents.
We are also committed to doing what we can — in light of who we are — to accelerate a sustainable pathway to a low carbon future. In one regard, this means leveraging the impact of our operating model through consolidation, and thereby accelerating a reduction of emissions within the natural gas production industry. In another, it means buttressing our efforts to reduce our emissions with carbon offset creation opportunities. In addition to generating credits that could be attached to our products to facilitate the establishment of differentiated products markets, we believe that opportunities exist for us to create offsets through activities that are consistent with our core competencies.
Additionally, while our net zero target does not include our Scope 3 emissions, we are exploring ways to meaningfully impact the emissions impact of the use of the products we sell and of others in the industry. As we noted above, our recent technological and cultural transformation has instilled across our organization the mentality, approach and nimbleness necessary to adapt in dynamic environments. These changes have been intentional and were pursued in part to allow EQT to evolve. The reality is that we do not believe that setting a net zero Scope 3 emissions target at this time is the optimal manner for EQT to contribute to an acceleration of a sustainable pathway to a low carbon future. Our track record demonstrates, for instance, that we can advance the rate of improvement in meeting a 1.5-degree scenario through consolidation, though consolidation would inherently attribute to our Company Scope 3 emissions of any future acquired company (emissions that would exist even if they were not acquired by us). We believe that advancing the collective goal of prevailing climate science should be the driving factor in shaping our strategy, and we will do just that.
To that end, we believe that we will have a competitive advantage in emerging energy transition technologies, many of which may not directly affect our reported emissions but still further this collective goal. We believe that our leadership has a demonstrable leading-edge track record in assessing and commercializing emerging technologies. When combined with being the largest producer of low-cost, low-carbon intensity natural gas, we believe we have a competitive advantage as a primary energy source for helping to decarbonize the domestic grid.
We believe these goals provide the right pace and targets to guide our strategy and decision-making throughout the Company, will continue to position EQT as a leader and the energy industry, and will accelerate a sustainable pathway to a low carbon future.
[1] EQT is subject to the methodologies for reporting GHG emissions under Subpart C (Stationary Fuel Combustion) and Subpart W (Petroleum and Natural Gas Systems) of the EPA Greenhouse Gas Reporting Program. We calculate our Scope 1 GHG emissions using EPA calculation guidelines under 40 CFR Part 98 Subpart Q. Under this Rule, hydrofluorocarbons, perfluorinated chemicals, sulfur hexafluoride and nitrogen trifluoride are not expected to be emitted in this sector. Our Scope 1 GHG emissions figures include all of our Scope 1 GHG emissions, regardless of size. Subpart W only requires certain GHG emissions to be reported to the EPA if the emissions exceed a certain specified level, so in some cases our Scope 1 GHG emissions disclosed in this report may be greater than the amount we report to the EPA. Additionally, although not shown in our total Scope 1 GHG emissions figure, we had 6,326, 4,721 and 3,782 metric tons carbon dioxide equivalent (CO2e) attributable to our fleet operations in 2018, 2019 and 2020, respectively.
[2] Our 2018 emissions figures include emissions from our midstream operations that were subsequently transferred to Equitrans Midstream Corporation in connection with the spin-off of Equitrans Midstream Corporation as a separate, publicly traded corporation in November 2018.
[3] Combustion emissions include emissions from our diesel and natural gas drill rigs, completion engines, stationary engines, reboilers, gas processing units (GPUs), vapor destruction units (VDUs) and generators.
[4] Process emissions originate from our glycol and desiccant dehydrators.
[5] Other vented emissions include emissions from our storage tanks, reciprocating compressors, well liquid unloading operations, pneumatic controllers and pumps.
[6] Fugitive emissions include equipment leak surveys and population count emissions.
[7] For purposes of this report, we use the AXPC’s definition of “flaring,” which is the flaring of wellhead gas from the primary separator at assets operated by EQT. This definition of flaring specifically does not include (i) combustion of low-pressure gas volumes from crude oil/condensate and produced water storage vessels or other low-pressure separators for the purpose of controlling emissions, or (ii) flaring from drilling and/or well completion, which are either (a) exempt from reporting to the EPA (e.g., flaring gas during the drill-out phase of completing a well), or (b) disclosed in our EPA emissions inventory reports under emissions from other sources (e.g., flaring associated with the operation of VDUs is captured under combustion emissions, and flaring associated with the operation of glycol dehydrators is captured under process emissions). For further discussion of our venting and flaring practices, see Venting/Flaring Practices.
[8] In prior years we have calculated our intensity metrics using net production of hydrocarbons as the denominator in the calculation. We have decided to switch to using gross production of hydrocarbons as the denominator for our intensity metrics, beginning with this year’s report. While there is no standard formula for calculating emissions intensity, we believe gross production is a more accurate representation for calculating our intensity, because gross production is a measure of the actual volume of hydrocarbons produced from the wells we operate. Accordingly, we have restated our 2018 and 2019 Scope 1 GHG emissions intensity metrics using gross production as the denominator in the calculation. We have also provided our net production volumes in the Corporate Profile section of this report, in the event a reader desires to calculate our intensity metrics using net production.
[9] Scope 2 emissions include only indirect emissions from EQT’s operations — does not include possible indirect emissions associated with the Chevron Assets.
[10] Scope 3 emissions include only indirect emissions from EQT’s operations, and exclude possible indirect emissions associated with the Chevron Assets.
[11] We presented these findings to the EPA in November 2020 in part to assist in their analysis on how to best tackle pneumatic device emissions.
Risk Management
At EQT, risk management has historically been decentralized, and we are currently reorganizing our approach to create a consolidated risk function, overseen by a designated risk leader. Doing so will enable us to coordinate between risk assessment functions and establish a consistent language and methodology across groups.
To ensure we are aligned and aware of our business risks, we survey senior leaders annually to assess Tier 1 enterprise risks. Based on this survey, we create a list of our top risks and present this information to our Board of Directors on an annual basis. We also conduct quarterly follow-up assessments to re-rank top risks and identify new or more effective measures for mitigation.
Our Financial group frequently uses models to assess the impact of our identified risks. This includes financial modeling, as well as commodity forecasting. For climate change specifically, we consider risk to our business, including demand for natural gas, renewables and other energy sources. In the first half of 2021, we built a proprietary emissions model that will be integrated with our financial model which will help us better understand carbon pricing and enable us to make business decisions based on both financial and climate impact. As we consolidate our risk function, we also plan to more explicitly incorporate transition and physical risks associated with climate change into our analysis.
Understanding the climate change risks and opportunities relevant to our business is fundamental to our ability to operate. In addition to setting reduction targets for our Scope 1 and 2 emissions, we are exploring new ventures and researching alternative technologies to further assist in decarbonization. We believe that natural gas will play a critical role in the energy transition and for that reason have engrained our climate strategy into our corporate strategy. For more information on our corporate strategy, please see Sustainable Value Creation.
Governance
Two Board-level committees contribute to setting our direction with respect to Environmental, Social and Governance (ESG) matters. The Corporate Governance Committee and the Public Policy and Corporate Responsibility (PPCR) Committee of our Board of Directors are responsible for approving, and making changes to, our ESG strategy, including reviewing our climate strategy and emissions targets. As part of its mandate to provide oversight of our ESG strategy, the PPCR Committee specifically considers climate change issues when developing, reviewing and assessing our ESG strategy in coordination with the Corporate Governance Committee and our ESG Committee. In 2020, we updated our PPCR Committee Charter and Corporate Governance Committee Charter to explicitly include oversight of ESG issues.
Our Vice President, Environmental, Health and Safety, and General Counsel provide updates on our GHG emissions and reduction initiatives to the PPCR Committee at least quarterly. In response to such updates, the PPCR Committee provides comments and feedback on our GHG management and emissions reduction initiatives, which are relayed to our ESG Committee for further consideration.
Our ESG Committee, comprised of our Chief Executive Officer, General Counsel, Chief Financial Officer and other senior leaders, meets biweekly and supports the Corporate Governance and PPCR Committees in helping to guide and ensure execution of our ESG strategy. The ESG Committee also assists our executive team and senior management in developing, implementing and monitoring initiatives, processes, policies and disclosures in accordance with our ESG strategy. In combination with the Board and Board Committee oversight described above, the ESG Committee provides input to the Board on strategic direction and works with senior management and specific business departments to coordinate the implementation and execution of our ESG strategy company-wide.
Our business departments, including our Environmental, Production, Finance and Business IT teams, work collaboratively to explore and implement new technologies to collect, report, forecast and reduce our emissions in line with initiatives established by our ESG Committee. Oversight of these initiatives is managed through our digital work environment and monitored by our ESG Committee.